Franska Solar Energy Institute Ines har utvecklat nya PV -moduler med termoplast och naturliga fibrer som kommer i Europa, såsom lin och basalt. Forskarna syftar till att minska miljöavtrycket och vikten av solpaneler, samtidigt som man förbättrar återvinning.
En återvunnen glaspanel på framsidan och en linnekomposit på baksidan
Bild: GD
Från PV Magazine France
Forskare vid Frankrikes National Solar Energy Institute (INES)-en uppdelning av de franska alternativa energierna och Atomic Energy Commission (CEA)-utvecklar solmoduler med nya biobaserade material i fram- och baksidan.
"Eftersom koldioxidavtrycket och livscykelanalysen nu har blivit väsentliga kriterier i valet av fotovoltaiska paneler, kommer inkallningen av material att bli ett avgörande element i Europa under de närmaste åren," sade Anis Fouini, chef för CEA-in-inses , i en intervju med PV Magazine France.
Aude Derrier, forskningsprojektets koordinator, sa att hennes kollegor har tittat på de olika materialen som redan finns, för att hitta en som kan göra det möjligt för modultillverkare att producera paneler som förbättrar prestanda, hållbarhet och kostnad, samtidigt som de sänker miljöpåverkan. Den första demonstranten består av Heterojunction (HTJ) solceller integrerade i ett allkompositmaterial.
"Framsidan är gjord av en glasfiberfylld polymer, som ger transparens," sade Derrier. "Den bakre sidan är gjord av komposit baserat på termoplast där en vävning av två fibrer, lin och basalt, har integrerats, vilket kommer att ge mekanisk styrka, men också bättre motstånd mot fuktighet."
Linen kommer från norra Frankrike, där hela det industriella ekosystemet redan finns. Basalten kommer från någon annanstans i Europa och är vävd av en industriell partner till INES. Detta minskade koldioxidavtrycket med 75 gram CO2 per watt, jämfört med en referensmodul med samma effekt. Vikten optimerades också och är mindre än 5 kg per kvadratmeter.
"Denna modul riktar sig till taket PV och bygger integration," sade Derrier. ”Fördelen är att den är naturligt svart i färg, utan behov av ett backark. När det gäller återvinning, tack vare termoplast, som kan omrelas, är separationen av skikten också tekniskt enklare. ”
Modulen kan göras utan att anpassa aktuella processer. Derrier sa att idén är att överföra tekniken till tillverkare utan ytterligare investeringar.
"Det enda imperativet är att ha frysar för att lagra materialet och inte starta hartsbindningsprocessen, men de flesta tillverkare använder idag prepreg och är redan utrustade för detta," sade hon.
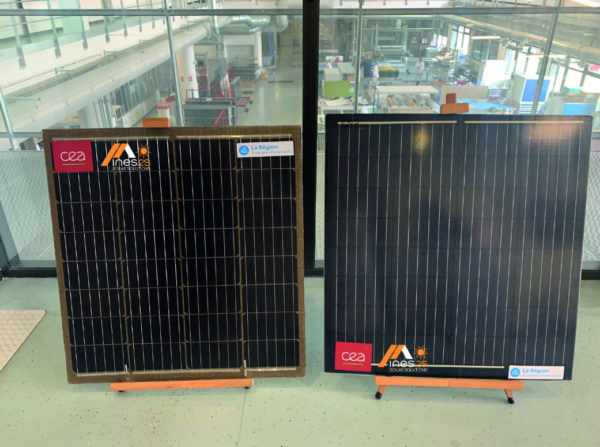
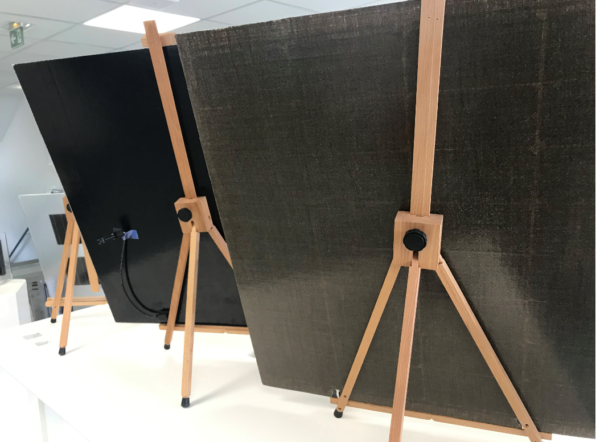
"Vi arbetade på det andra livet i glas och utvecklade en modul som består av återanvänt 2,8 mm glas som kommer från en gammal modul," sade Derrier. "Vi har också använt en termoplastisk inkapslingsmedel som inte kräver tvärbindning, vilket därför kommer att vara lätt att återvinna, och en termoplastisk komposit med linfiber för motstånd."
Modulens basaltfria bakre yta har en naturlig linnfärg, som till exempel kan vara estetiskt intressant för arkitekter när det gäller fasadintegration. Dessutom visade INES -beräkningsverktyget en minskning med 10% i koldioxidavtrycket.
"Det är nu absolut nödvändigt att ifrågasätta de fotovoltaiska leveranskedjorna," sade Jouini. ”Med hjälp av Rhône-Alpes-regionen inom ramen för den internationella utvecklingsplanen letade vi därför efter spelare utanför solsektorn för att hitta nya termoplast och nya fibrer. Vi tänkte också på den nuvarande lamineringsprocessen, som är mycket energiintensiv. ”
Mellan tryckskapet, pressningen och kylfasen varar lamineringen vanligtvis mellan 30 och 35 minuter, med en driftstemperatur på cirka 150 ° C till 160 C.
"Men för moduler som i allt högre grad innehåller ekodesignade material är det nödvändigt att omvandla termoplast till cirka 200 ° C till 250 C, med vetskap om att HTJ-tekniken är känslig för värme och inte får överstiga 200 C," sade Derrier.
Forskningsinstitutet samarbetar med Frankrike-baserad induktion av termokomtressspecialist Roctool, för att minska cykeltiderna och göra former enligt kundernas behov. Tillsammans har de utvecklat en modul med en bakre yta gjord av termoplastisk komposit av polypropylentyp, till vilken återvunna kolfibrer har integrerats. Framsidan är gjord av termoplast och glasfiber.
"Roctools induktion av termokomtressprocessen gör det möjligt att värma de två främre och bakre plattorna snabbt, utan att behöva nå 200 C i kärnan i HTJ -cellerna," sade Derrier.
Företaget hävdar att investeringen är lägre och processen kan uppnå en cykeltid på bara några minuter, medan de använder mindre energi. Tekniken riktar sig till sammansatta tillverkare, att ge dem möjlighet att producera delar av olika former och storlekar, samtidigt som de integrerar lättare och mer hållbara material.
Posttid: jun-24-2022